
Build area 3 - EXTREME - GREEN - POWER
ELECTRIC - HYDROGEN - E FUEL
BUILD PARTNER - POWER UNIT - 1 PER FUEL TYPE
BUILD BRAND PARTNER - SELECT THE PARTS YOU CAN MAKE
Build Area Highlight: Body Design & Components – POWWWWWEEERRRRRR
The Kill All Metal Series 1 builds are engineered to educate, innovate, and push the boundaries of sustainable performance. This is not just about creating fast cars—it’s about proving the real-world potential of EV, E-Fuel, and Hydrogen powertrains, showing how they are made, how they perform, and what their future holds.
This is where we separate hype from reality—where engineering, science, and raw performance collide to give the world a definitive answer on what the future of green performance truly looks like.
The Powertrain Challenge: Engineering the Future of Performance
Our mission is to take a standard 215bhp hot hatch engine and re-engineer it into an F1-powered monster, showing the world what happens when cutting-edge materials, manufacturing, and engineering are applied to a road-going vehicle.
Here’s how we push each powertrain to its limits:
-
Revolutionizing the Engine
-
Transform a 215bhp production engine into an 800-1000bhp power unit using extreme modifications to the block, internals, and components.
-
Explore new materials such as recycled aluminum, advanced composites, metal 3D printing, and laser-weld printing to make manufacturing faster, cheaper, and more sustainable.
-
Show the entire digital design and simulation process before manufacturing, testing, and assembly.
-
-
Manufacturing That Defines the Future
-
Feature sterile, ultra-modern assembly environments, showcasing both robotic automation and expert hand-assembled precision.
-
Work with industry leaders to develop, test, and validate powertrain modifications that push performance, efficiency, and environmental impact.
-
Introduce groundbreaking production techniques such as metal additive manufacturing and precision machining to reduce waste and improve efficiency.
-
-
Proving It on the Track
-
Three powertrains—EV, E-Fuel, and Hydrogen—battle in head-to-head racing across multiple disciplines, from drag racing to endurance and time attack.
-
We analyze:
-
Performance: 0-60, top speed, lap times.
-
Efficiency: How long it takes to fill or charge, energy cost per mile.
-
Usability: How each powertrain feels, sounds, and performs in real-world conditions.
-
Environmental Impact: What it takes to make and sustain each fuel type.
-
-
-
Technical Collaboration & Brand Integration
-
This build area is ideal for manufacturers with in-house powertrain and engine-building capabilities.
-
However, there is an option to collaborate with existing performance engine specialists such as Cosworth, Yamaha, or other high-performance engineering firms.
-
Brand partners will receive full digital exposure as we document the engineering, manufacturing, and real-world validation process.
-
To summarise - there is room for 3 power train manufacturers.
Take a pre existing engine design , modify to accept hydrogen & e fuel , create a EV power unit that is lower impact on the environment like sodium ion and use doughnut labs axial motors.
The for the combustion engine - completely re manufacture every part using space age exotic materials and manufacturing processes , make it 1000bhp if possible by boring if needed , the 1.6l turbo charged 4 cylinder petrol engine can be modified and made in any way the target is to absolutely revolutionise this engine
There is an option to work with high performance manufacturers with a role of heading up each parts production , this basically means you specify / design digitally and they manufacture. All we want from this exercise is show off your technical ability by giving the perception that you are talented enough to build anythiing and make it world record breaking.
What We Need from Our Build Partner
To execute this challenge, we need a high-level engineering partner that can:
✅ Handle digital design & simulation before manufacturing.
✅ Modify, test, and validate powertrain components with the latest technology.
✅ Manufacture engine and powertrain components in-house or collaborate with suppliers.
✅ Provide industry-leading expertise in high-performance engine development.
✅ Deliver educational content on materials, technology, and processes for global STEM audiences via the Ultra E app.
All components are available to the public once tested on the show
To ensure further support to our build partners beyond the marketing & endorsement value, Every part that is safe to will be retailed to the market, for the show the components can be made higher risk and more exotic but for retail the components can be less exotic and safer , all parts are being made as motorsports, the retail sales will be from the KILL ALL METAL store and we carry the liabilities and insurances, however the retail sales have not be created to be a money making process for the show, it has been created to provide higher levels of value for each build partner.
While you are able to apply for R&D refunds to recoup costs spent on developing parts for the show, we have added the retail arm of the show to sell the high performing parts world wide to industry and retail, this will generate exponentially more than any investment you placed in to parts development.
Currently the record is set at 715bhp for this engine without Nitrous oxide and without the engine being completely developed.
Why This Build Area is Critical
This project isn’t just about building a car—it’s about delivering a blueprint for the future of performance engineering. This is the most advanced powertrain battle ever created, designed to inspire, educate, and redefine what the automotive world considers possible.
This is a once-in-a-lifetime opportunity to showcase your company’s full expertise in engineering, powertrain development, and sustainable innovation.
This is your chance to define the future of high-performance engineering. Let’s build the future—together.
take a look below at every part group needed to manufacture
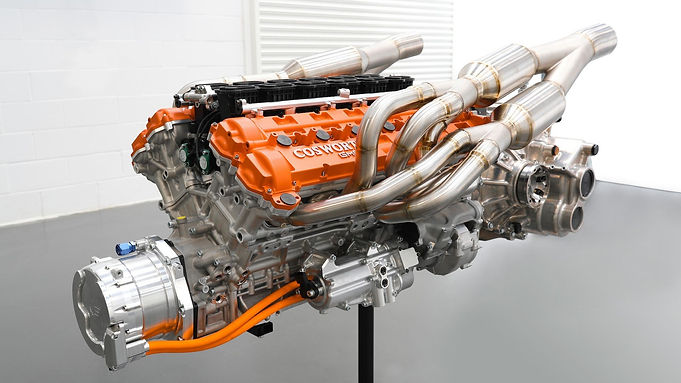
COMPONENT FEATURES / FUNCTIONS
Components and features
COMPONENTS TO BE MANUFACTURED WITH TARGET SPEC MANUFACTURING
To ensure each powertrain exceeds 1000BHP, remains as light as possible, and is indestructible under extreme stress, we must use exotic materials, advanced manufacturing techniques, and reinforced components. Below is a refined and high-performance parts list for each power unit, incorporating maximum efficiency, strength, and durability.
1 E-FUEL ENGINE
🔹 Modified & Strengthened Internal Combustion Engine Running on Synthetic E-Fuel
Engine Block & Cooling System
✅ Material: Billet 6061-T6 aluminum block (CNC machined), reinforced with titanium sleeves
✅ Manufacturing Technique: 5-axis CNC machining, plasma nitriding, & cryogenic treatment
✅ Cooling Enhancements:
-
Closed-deck block conversion for extreme boost pressure
-
Integrated oil jets & cryogenic intercooling system
-
Cooling fins machined into the block for added heat dissipation
-
Direct air cooling intakes (inspired by Koenigsegg Free-valve tech)
Cylinder Head & Valvetrain
✅ Material: Billet aluminum or Inconel 625 CNC-machined head for extreme heat resistance
✅ Upgrades:
-
Titanium hollow valves (DLC-coated) & sodium-filled exhaust valves
-
Pneumatic valve springs (F1-style) to eliminate valve float at 10,000RPM
-
Roller finger followers & DLC-coated lifters for ultra-low friction
-
Custom camshafts optimized for high-RPM combustion efficiency
Pistons & Connecting Rods
✅ Material: Forged billet 2618 aluminum pistons, ceramic-coated
✅ Upgrades:
-
Graphene-coated skirts for friction reduction
-
Titanium con-rods with ceramic coating for extreme RPM loads
-
DLC-coated wrist pins for high-load endurance
Crankshaft & Bearings
✅ Material: Billet 4340 chromoly steel or titanium crankshaft (lightweight & ultra-strong)
✅ Upgrades:
-
Knife-edged counterweights for reduced rotational drag
-
Plasma-Nitrided bearings for extreme pressure resistance
Turbocharging System
✅ Setup: Twin-scroll turbo with electric assist (Garrett G42/58 or BorgWarner EFR Series)
✅ Cooling: Methanol injection, liquid-cooled charge pipes, intercoolers with cryogenic cooling
✅ Wastegate & BOV: Titanium external wastegate for extreme heat durability
Fuel System & Ignition
✅ Hybrid direct & port injection system (Koenigsegg-inspired Free-valve tech)
✅ Methanol-compatible high-pressure injectors (2200cc+ flow rate)
✅ Dual-stage fuel pumps with cryogenic cooling system
2 HYDROGEN SYSTEM
🔹 Ultra-efficient, high-RPM hydrogen-adapted engine with reinforced internals
Engine Block & Head Modifications
✅ Material: Reinforced billet aluminum block with ceramic thermal coating
✅ Upgrades:
-
Lower compression ratio (9:1) to prevent pre-detonation
-
Plasma-coated combustion chambers to resist hydrogen flame speeds
-
High-flow, low-friction valve train (titanium valves & camshafts)
Hydrogen-Specific Components
✅ Hydrogen direct-injection system (ultra-high-pressure fuel rails & injectors)
✅ Plasma ignition system for rapid combustion efficiency
✅ Advanced turbocharging system with water-methanol cooling to prevent NOx buildup
Cooling & Safety Enhancements
✅ Cryogenic hydrogen injection cooling system
✅ Hydrogen-specific knock sensors and detonation prevention mapping
✅ Triple-layer hydrogen fuel tanks with reinforced containment
3. EV Powertrain – 1000BHP+ Electric with Axial Motors
🔹 Ultra-light, high-power AWD EV system using axial flux motors for extreme efficiency & performance
Electric Motors & Drivetrain
✅ Motors: 4x Doughnut Labs Axial Flux Motors (one per wheel, each rated at 250-300BHP)
✅ Weight: Each motor weighs only ~28kg, providing the highest power-to-weight ratio possible
✅ Cooling: Liquid-cooled with active heat dissipation
✅ Mounting: Custom carbon-fiber reinforced aluminum motor mounts
Battery System
✅ Type: 800V solid-state battery pack with graphene ultracapacitors
✅ Weight Reduction: Optimized for minimum mass using aerospace-grade materials
✅ Fast Charging: 800kW ultra-fast charging (0-80% in under 10 min)
Inverter & Power Electronics
✅ Silicon carbide-based ultra-high efficiency inverter
✅ Custom DC fast-charging module
✅ Integrated AI torque vectoring system
Cooling & Thermal Management
✅ Active heat exchanger for battery cooling
✅ Liquid cooling for inverters & motors
Manufacturing Techniques for All Powertrains
To achieve 1000BHP+ reliably, we must utilize the latest high-performance manufacturing techniques:
🚀 CNC Machining (Billet Aluminum & Titanium Components)
🚀 Metal 3D Printing (Titanium Exhaust, Inconel Turbo Manifold)
🚀 Laser Weld Printing (Lightweight & High-Strength Block & Heads)
🚀 Cryogenic Treatment (For Hardening Critical Load-Bearing Components)
🚀 Plasma Nitriding (For Extreme Durability in Crankshaft & Bearings)
Final Summary: components
Each power unit requires a bulletproof combination of lightweight, high-performance materials and precision engineering.
🔹 E-Fuel Engine: - N14 engine 1.6l to be modified / re engineered
✅ Billet CNC-machined block & head
✅ Titanium rotating assembly
✅ Ultra-high-performance turbocharging
✅ Methanol-injection hybrid fuel system
🔹 Hydrogen Engine: n14 engine 1.6l to be modified / re engineered
✅ Reinforced billet block with plasma-coated chambers
✅ Hydrogen-specific fuel injection & ignition system
✅ Advanced safety & cooling systems
🔹 EV Powertrain: chassis floor /boot floor cut / motors placed
✅ 4x Doughnut Labs axial motors (AWD setup)
✅ 800V graphene-enhanced solid-state battery
✅ Silicon carbide ultra-high efficiency inverter
✅ AI torque vectoring & regenerative braking system
The Mission: Delivering Unbreakable 1000BHP+ Power Units
This finalized shopping list ensures that all three powertrains will be as powerful, lightweight, and indestructible as possible. Each system is engineered for peak performance, durability, and efficiency, using cutting-edge materials and manufacturing techniques.
This should provide a clear roadmap for what needs to be designed, re-engineered, and fabricated, ensuring Kill All Metal delivers the most extreme multi-fuel performance challenge ever seen.
🚀 Let’s build the future—together. 🚀